In late September, as part of the Future of Surfactants Summit North America, our development chemist Dr Alex Papiez and I were given the opportunity to visit the LEED platinum-certified Method factory in Chicago, where they are setting new standards for making household cleaning products.
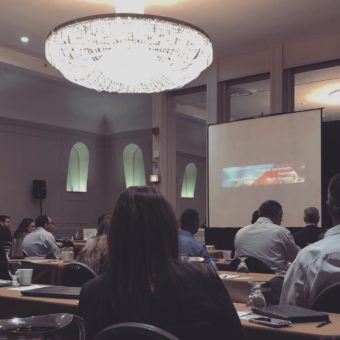
I’ve been fascinated by the inspirational Method story ever since they burst onto the clean scene in the early 2000s. So, when the chance to look inside the South Side Soap Box came along, we jumped at it.
THE METHOD FACTORY
Located in the South Side of Chicago, Method’s manufacturing home (The South Side Soap Box) has been designed to be sustainable from the ground up, to express the company mission at every scale. Built on a rehabilitated brownfield site, the factory is a clean home; with a wind turbine, solar trees in the factory car park and a 75,000-square-foot climate-controlled growing roof (managed by Gotham Greens) paving the way for the future of urban agriculture. It also has a basket-ball court in the production area!
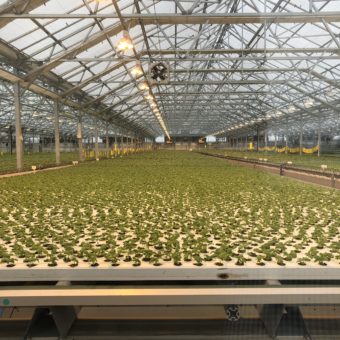
When Method decided to design and build their soap factory, they knew it had to be special, and they focused on using clean energy, water and materials to create their household products. They wanted the highest levels of efficiency and sustainability available. They wanted their packaging manufacturer and distribution centre all under the same roof to reduce their carbon footprint, and they wanted to build in an area where they’d have the opportunity to contribute to its future, bringing 100 manufacturing jobs to a community in need of employment opportunities!
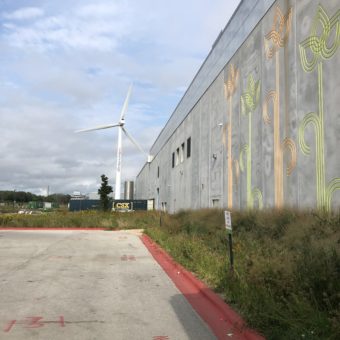
In April 2015, 18 months after breaking ground in Chicago’s historic Pullman Park district in South Side Chicago, they opened the doors to the industry’s first LEED-platinum certified plant.
The Method factory we walked around couldn’t have been further from the traditional image of a gritty urban factory – and we were very impressed by everything they’ve achieved so far. The owner, Adam Lowry explains: “We wanted to become native to an urban community and create an example of what manufacturing can look like in the 21st century. This building is a signal of Method’s intention to be part of a positive future.”
We learned so much from the two-day summit in downtown Chicago, and the factory tour… and we’re now even more inspired to continue improving everything that we do at Ideal’s manufacturing home in Northamptonshire. Watch this space.
Meanwhile, if you’re interested to find out more about the Method story, I’d recommend reading The Method Method – written by the founders Adam Lowry and Eric Ryan in 2011.
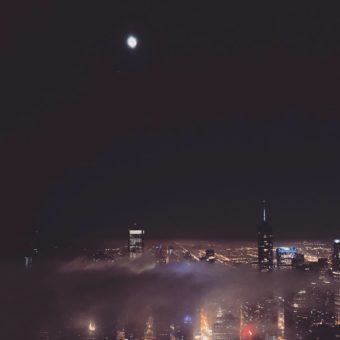