We spoke to our chairman, founder and original laundromatinee idol, Dr Michael ‘Magic Mix’ Kalli, about Ideal’s role and contribution to the transformative changes that have taken place since 1975 and the necessary additional changes coming to us and (hopefully) the industry at large.
Where It All Began
So, how did you start out in formulation?
After finishing my PhD, I found employment as the chief chemist for a company supplying cleaning and hygiene products to all kinds of industries. Part of my duties were to support field personnel to help resolve problems encountered in various industrial sectors: breweries, dairies, food manufacturers. This gave me a good insight into product application and formulation chemistry.
You must have had a breakout moment, though, right?
On just such a mission I was talking to the chief scientist of a large food processing company, who asked if I could help with a serious issue they were experiencing regarding stain removal from heavily soiled garments at one of the professional laundries in their group.
I put together a bucket of what I considered appropriate for organic stain removal which contained enzymes, surfactants, quaternary ammonium salts and oxidising agents and I set off to help.
Those things are all taken for granted now, though. What did you think of the state of things at the time, as a chemist, and what impact did your formulation have?
My first impression of the laundry process was how lacking in technical awareness the operatives were about what they were doing! Water, energy and labour was cheap and they used it in abundance. Moreover, there was very little awareness of environmental impact, chemical hazard or pollution issues.
I surprised both them and me when we discovered that we could get an excellent result in one single wash cycle of 15 minutes and a couple of rinses!
Their old process involved up to four wash cycles and four rinses. I realised we could save huge mounts of resource and achieve a much better result.
Interestingly, what I was doing was in total contravention to the accepted BLRA laundry processing manual, but I reckon that must have been compiled in the 17th Century!
Ha! Alright. So how does this all lead to commercial success? We’re supposed to be talking about your big break!
The product I decided to move into the industry with, which was basically the product I tested above was called Nova LP.
I saw it as an exciting opportunity and went on to create my own company on the back of it, supplying products and advice that would help transform the industry. Without financial resource things proved a little difficult so I negotiated a factoring agreement (a means of creating unlimited and unrestricted growth), contract manufacture of a range of products and a way to buy raw materials without credit guarantees.
So that’s the beginning of Ideal, then? Or was there more to it than that?
I set about communicating this breakthrough to the major players in the industry at the time; Initial, Sunlight, Spring Grove Services and Sketchley.
The company achieved a turnover in excess of £1m in the first year and before long, several competitors had arrived on the scene, eager to enter the new market.
We went on to introduce means by which launderers could simply, but very effectively, assess performance and quality whilst enabling clear savings in water consumption, energy use and effective stain removal. However, the issues with labour prevailed as personnel were employed purely to ensure the right amount of product went into the machine at the right time. Which, of course, was also the cause of many process issues that sometimes resulted in bad quality.
Sounds like a big issue to fix in the pre-2k world. How did you overcome that?
We were the first to create an automated injection system for metering the necessary product mix into a machine, to get great wash results! This was based on my experience with other industries and we started formulating liquid products for metered injection into laundry machines. Laundry operatives were no longer tied to an old fashioned function and consistent, optimal additions could be guaranteed (most of the time!)
That was back in the early eighties and of course, loads has happened since then, both in terms of the people & businesses involved in this kind of activity and the nature and level of automation of handling and finishing equipment, along with computerised auto dosing of products.
…and it looks like we’ve been continuing along those lines ever since. But what really comes next? What do you think the next big play is for the industry?
The need to minimise energy use and eliminate micro-fibre discharge into effluent. That’s become majorly important for a number of reasons including linen life and most importantly because of serious environmental & health concerns.
One of the key factors of high micro fibre discharge in the laundry industry is the absolute need to disinfect linen at the final stage of the process. Hitherto, it’s been common practice to thermally disinfect, particularly in respect to institutional laundries. Developments are taking place in surfactant chemistry and activated oxidising agents that are pushing down the levels of micro fibre discharge by lowering temperatures of processing to remove soiling of all types. But, it is still massively important to validate any disinfection process.
Currently, other than thermal disinfection as a means of validated disinfection in the laundry process there’s the use of a substituted phenolic derivative of peracetic acid.
We embarked on our own mission to enable a novel means of effective disinfection of linen during the worst of the covid-19 period and secured two prestigious government grants to carry out research in conjunction with Northumbria University. We have shown in laboratory experiments that we can formally disinfect at ambient temperatures using ozone, but we have not been able to partner with a commercial outlet to validate our results in practical situations… yet!
Thanks, Mike. It’s great to give people this kind of overview.
Any time, Andrew.
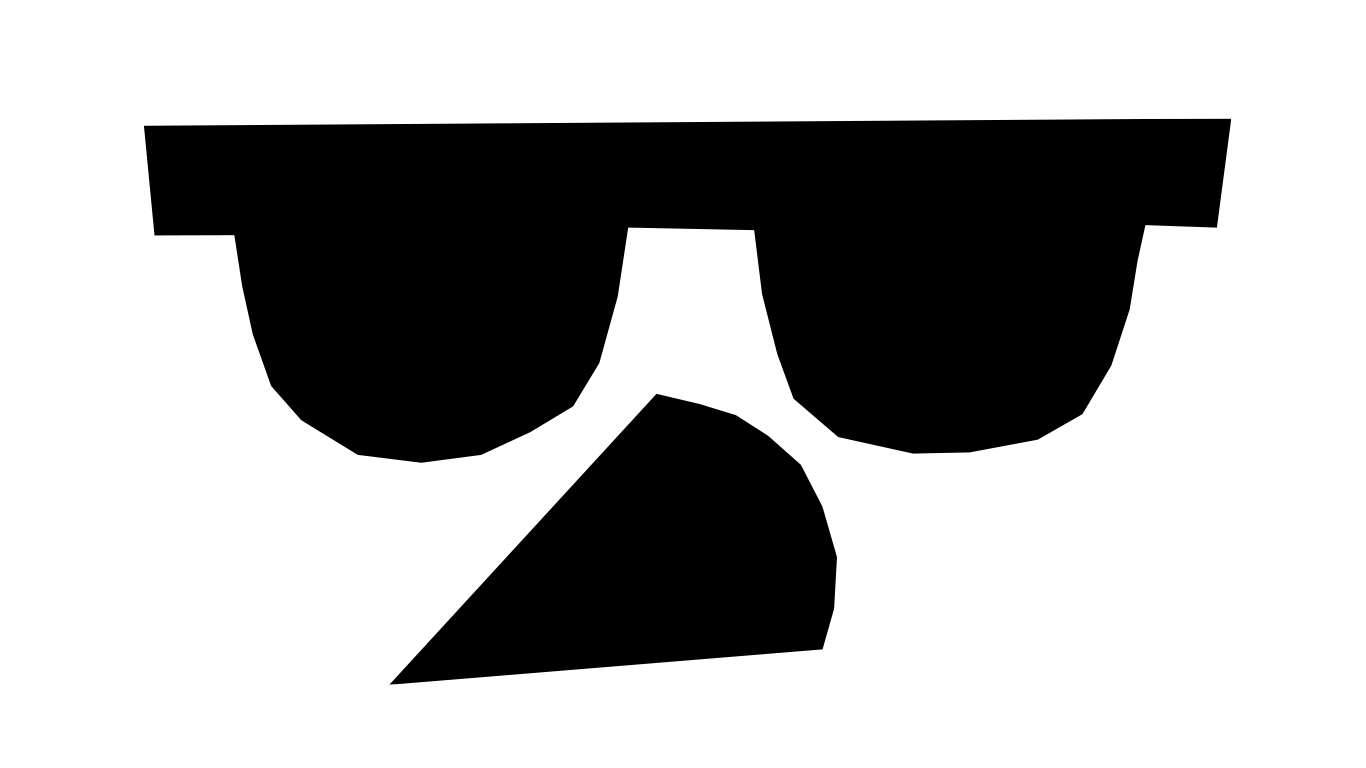
About This Series
We hope you found this useful! This is part of a series of blog posts about our values and what means the most to us. Keep checking back and take a look at our laundry science blogs for an in-depth look at what makes a laundry tick